Lean Production is all about finding the most efficient ways to use resources and cut down waste. In manufacturing, this concept can be extremely powerful when combined with robotic automation.
Modern manufacturing technology is continually evolving. If you want your manufacturing company to stay ahead of the curve, you need to implement the right strategies to keep up with these changes.
Robotics has been a pivotal component in Lean Production since at least the 1980s if not before. In a Lean Manufacturing environment, you can use robots to decrease downtime, reduce wasted effort, and improve resource utilization.
But, how can you combine robotics effectively with Lean Production when using RoboDK?
Let’s look at the essentials of Lean Production and how you can get the most from your robot.
The History and Evolution of Lean Production
The concept of Lean Production has its roots as far back as the 1450s. Around this time in Venice, Italy, a naval shipyard called the Venetian Arsenal pioneered the use of a standardized process for shipbuilding with continuous production flow.
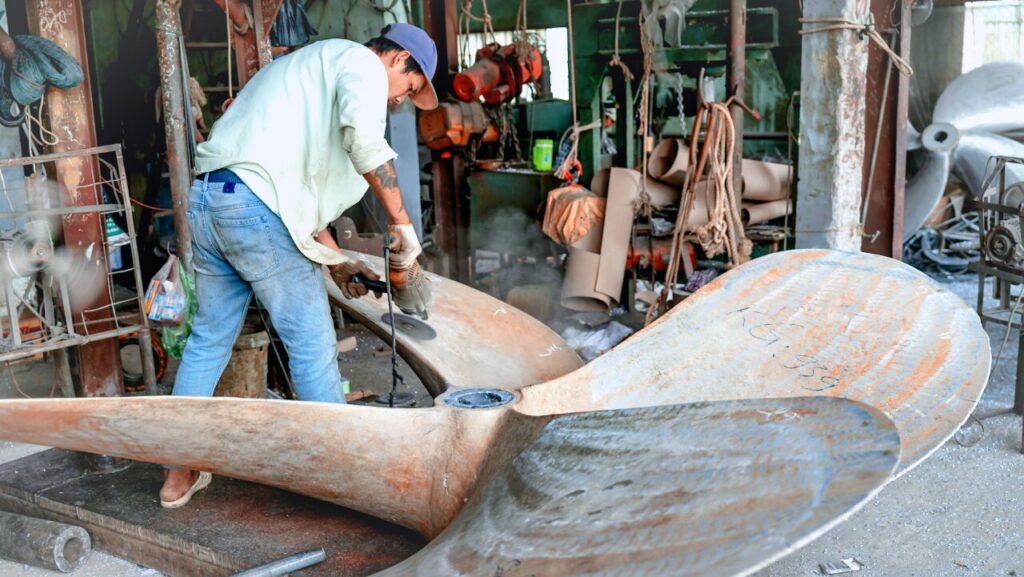
But the Lean Production that we know today really began its journey in 1913 with Ford’s invention of the Model T automobile. His factory concepts laid the groundwork for the Toyota production System, which was the basis for modern Lean Production.
It is based on the concepts of defining customer value, mapping the value streams, and smoothing production flow. The methodologies and systems first developed at Toyota have since moved beyond manufacturing. Lean concepts are now used in a variety of sectors, including logistics, healthcare, and government.
Robots have played an integral role in the evolution of this concept. Since the first industrial robot, the Unimate, in the 1960s, automation has gradually become a common tool for implementing Lean principles.
5 Key Principles of Lean Production and Where Robots Fit
One way to understand Lean Production is to break it down into 5 key principles.
Here are those 5 principles and where robots fit within them:
1. Identify Value Within Your Production
The first step is to identify where “value” is created within your manufacturing process. In Lean, value is something that is truly important to your customers. Adding value means that you add product or service features that matter.
Robots can carry out both value-added and non-value-added processes. However, many of the easiest “wins” with robotic automation come when you use them for processes that don’t add value. The robot itself becomes the technique to remove this waste.
2. Map the Value Stream
Value stream mapping involves identifying all the key steps that your product or service goes through before reaching the customer. It helps you to identify and remove those steps that don’t add value.
When you are using robots to support your Lean Production, a robot simulator, like RoboDK, can be a powerful asset at this stage. The simulator helps you to optimize your robotic workflows and identify inefficiencies in your production.
3. Create a Smooth Flow
A well-optimized Lean Production process has a smooth flow. This means that it does not create unnecessary inventory at any stage, or any other types of waste.
Robots often help to smooth production flow as you can program them to operate at a consistent rate. This can help to impose more regularity on the entire production flow. You can then use a tool like RoboDK to optimize the robot’s cycle time.
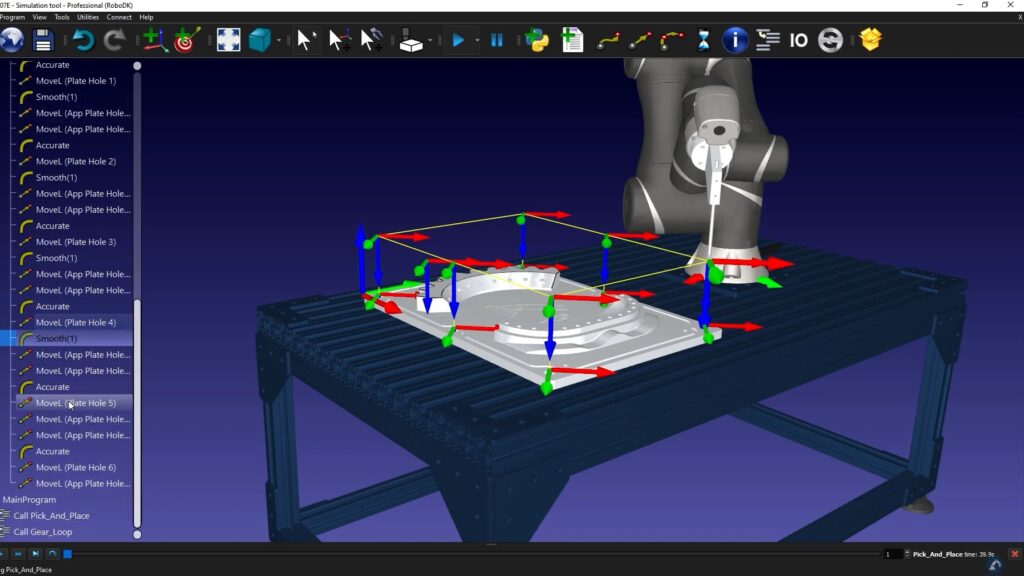
4. Establish a Pull System
Lean Production is based on the idea of creating a pull instead of a push system. Pull systems respond to the customer demand instead of creating unnecessary inventory “just in case.”
An important part of using robots in Lean is agility and scalability. With the right robot programming system, you can easily change your production on-the-fly to adapt to changing customer demands.
5. Strive for Perfection
The final key principle of Lean Production is easy… Be perfect.
Simple, right?
Of course, perfection is impossible in practice. There are always aspects of your process that you could improve, and this is the point. Lean Production operates on the principle of continuous improvement.
With RoboDK and robots, you can continue to optimize your robot deployment without disrupting production. You can improve your deployment in the simulator, then only program the physical robot when you have shown a measurable improvement.
5 Benefits of Lean Production Supported by Robots
Of course, you don’t need to use robots in a Lean Production system. The principles are applicable even when you use no automation at all.
However, there are some significant benefits to supporting your Lean Production process with robotics.
Here are 5 benefits to using robotics with Lean:
- Consistent Product Quality — Robots are exceptional at consistency. Every time you optimize part of your flow, these changes will remain and can lead to ever-increasing product quality.
- Sustainable Production — Reducing waste is a core part of Lean but is also important for improving sustainability. Robots are an effective way to reduce wasteful manual steps.
- Shorter Lead Times — Lead times are affected by various processes in your business. Robots can help you save time in a range of specific ways that can reduce lead times.
- Decreased Overheads — Eliminating unnecessary expenses and overproduction are critical parts of Lean. Robots can help you optimize your labor costs and reduce the cost of producing each product.
- Competitive Advantage — Ultimately, robots can help you stay ahead of the curve in your industry. By strategically using robots at key stages in your Lean Production, you can set yourself up to outshine your competitors.
Lean Production alone offers significant benefits compared to traditional production. However, when you combine Lean with robotics, you can gain that edge that makes a real difference.
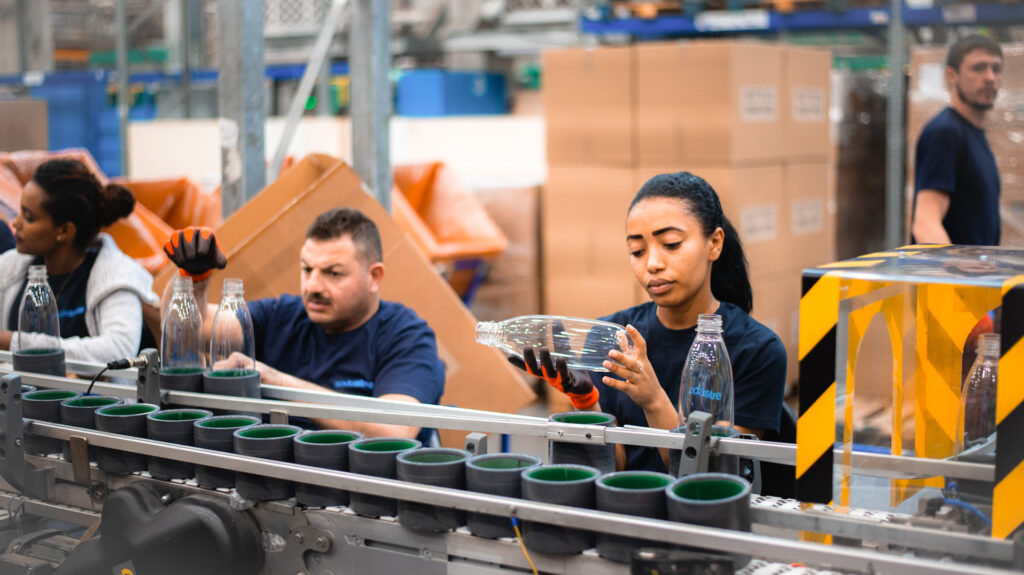
Use RoboDK to Optimize with Robots in Your Business
If we had to highlight just one key concept of Lean Production, it would be continuous improvement.
By committing to keep improving your production, you can make huge strides for years to come.
RoboDK is an excellent tool for continuously optimizing your robotic setup. Its powerful range of features provide you with many options for continuing to tweak and improve your deployment.
Which principle of Lean Production is most important to you right now? Join the discussion on LinkedIn, Twitter, Facebook, Instagram, or in the RoboDK Forum.. Also, check out our extensive video collection and subscribe to the RoboDK YouTube Channel